In the dynamic realm of Aftermarket Warehouse Distribution, precision, and efficiency reign supreme. The AutoPower Warehouse Management System (WMS) stands as an exemplar of excellence, seamlessly bridging the gap from single warehouse operations to the complexity of multi-warehouse endeavors. At its core, the WMS is a best-of-breed solution, meticulously crafted to meet the unique demands of the industry. Let’s delve into the multifaceted capabilities of the AutoPower WMS, designed to optimize your operations and elevate your warehouse management to unparalleled heights.
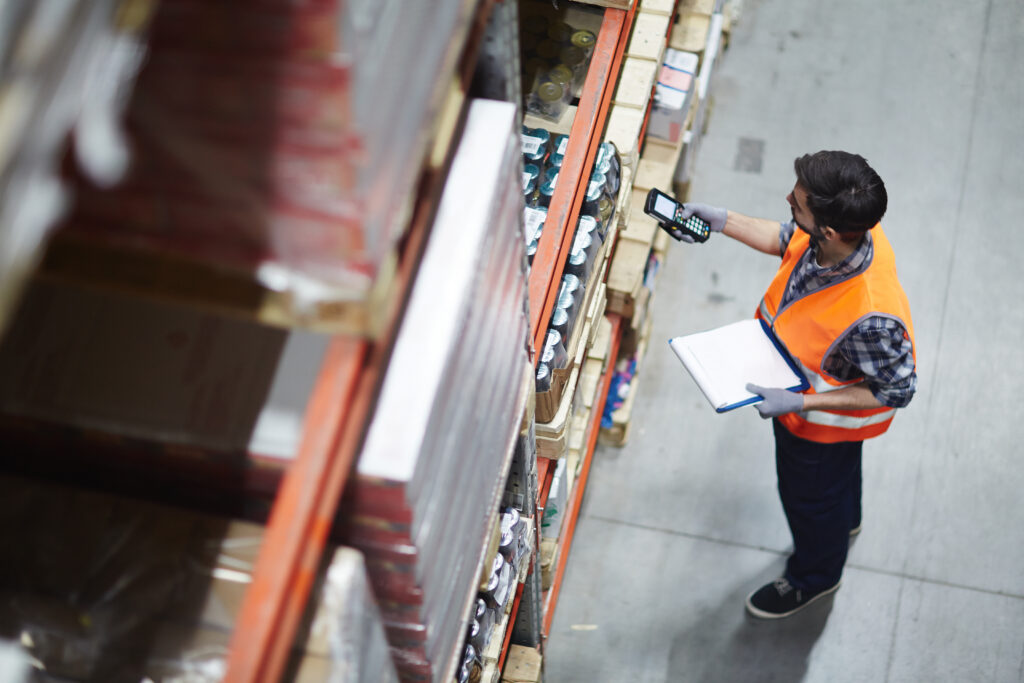
Innovative Features of the AutoPower Warehouse Management System
- EDI Advanced Shipping Notices (ASN): Seamlessly integrated, our WMS empowers you with real-time insights through advanced shipping notices from suppliers. Stay informed about backorders, estimated time of arrivals, and essential tracking information, allowing you to proactively manage your inventory flow.
- Bar Code Scanning for Precision: Embrace the power of bar code scanning, a cornerstone of modern warehouse efficiency. From seamless tracking of inventory movements to precise identification of raw materials, bar code scanning permeates every facet of your operations, ensuring accuracy, real-time visibility, and heightened productivity.
- Streamlined Put-Away and Returns Processing: Experience the seamless orchestration of put-away and returns processing, a crucial facet of warehouse inventory systems management. Efficiently allocate inventory to its designated location while effortlessly managing return processes, all orchestrated within the AutoPower WMS ecosystem.
- Efficient Core Returns: Simplify the complexity of core return management with our WMS. Gain comprehensive visibility into core inventory, streamline return processes, and ensure that core components are efficiently routed back into circulation.
- Effective Product Labeling: Every item within your inventory carries its unique identity. The AutoPower WMS empowers you to streamline product labeling, ensuring accurate identification, smooth traceability, and enhanced efficiency in inventory management.
- Strategic Bin Locations: Optimize your warehouse layout with strategic bin locations. Our WMS enables you to intelligently organize inventory within your warehouse, minimizing travel distances, enhancing picking efficiency, and ultimately boosting operational speed.
- Precision in Picking and Packing: Precision is the heartbeat of warehouse operations. The AutoPower WMS facilitates meticulous picking and packing processes, ensuring that orders are accurately fulfilled, reducing errors, and enhancing customer satisfaction.
Effortless Staging and Shipping: Seamlessly transition from packing to staging and shipping. Our WMS empowers you to orchestrate these critical stages with ease, minimizing bottlenecks, enhancing order throughput, and ensuring timely shipments.
Driving Efficiency through Inbound Management
Inbound Management stands as a linchpin of our Warehouse Inventory Systems, seamlessly intertwining inventory visibility with immediate data validation and verification. This synergy enables transformative process enhancements across inventory cycle planning, space utilization, and overall warehouse productivity. With the AutoPower WMS, you gain a vantage point that allows you to make informed decisions, optimize resource allocation, and navigate the complexities of inbound operations with confidence.
Leveraging Inbound EDI Advanced Shipping Notices (ASN)
The power of Inbound EDI Advanced Shipping Notices (ASN) is harnessed within our WMS. This functionality extends unparalleled pre-receipt visibility, equipping you with crucial insights into backorders, estimated time of arrivals, and comprehensive tracking information. The result? Enhanced operational agility, reduced uncertainty, and the ability to plan and strategize with precision.
Elevating Accuracy through Inventory Cycle Counting and Bar Code Systems
In the pursuit of operational excellence, precision is paramount. Enter the realm of inventory cycle counting and bar code systems. Delve into any competitive business, and you’ll find barcodes seamlessly integrated into warehouse inventory systems at every operational juncture. These unassuming labels hold the power to revolutionize your operations, accurately identifying raw materials, orchestrating seamless work-in-process tracking, and providing an enduring identifier for service and warranty management. The benefits are as profound as they are tangible – a workforce empowered by real-time visibility, a reduction in errors, and a leap in productivity.
Numerous Roads to Enhanced Efficiency
The profound impact of barcode systems manifests in myriad ways:
- A comprehensive study reveals that companies bolstering their Enterprise Resource Planning (ERP) with real-time automated data collection yield a staggering 50% higher return on their ERP investment compared to their counterparts.
- Warehouses fortified with wireless barcode input commonly achieve inventory accuracy rates hovering around 99.x%.
- Even the most experienced typists make one error approximately every 300 keystrokes. The simple act of replacing manual data entry with barcode scanning has a ripple effect – errors dwindle, operational efficiency soars and valuable labor is unshackled from the clutches of tedious data resolution.
A Clear Imperative for All Businesses
In the automotive industry’s intricate tapestry, every business, regardless of its scale, should seize the advantages of barcoding. This transformative technology liberates your workforce, reduces paperwork, and unleashes a cascade of efficiency gains across asset management, supplies, and shipments. It’s an imperative that transcends business models and operational paradigms.
Navigating the Path to Reliability with AutoPower
While the virtues of barcoding are evident, the journey to a reliable and effective barcode system demands a nuanced approach. This is where AutoPower’s installation and implementation expertise emerges as a guiding light. With years of experience and a deep understanding of the intricacies, we navigate the complexities of integrating barcode systems seamlessly into your operations. The result? A robust, reliable, and effective system that amplifies efficiency, accuracy, and operational agility.
Unveiling the Power of Order Management
In the intricate dance of warehouse management, order visibility reigns supreme. The AutoPower WMS is your steadfast ally, providing a panoramic view of inventory, orders, backorders, and work orders. This invaluable insight forms the bedrock of optimal workload planning, staffing efficiency, heightened order throughput, and refined warehouse planning. With AutoPower’s Warehouse Inventory Systems, you’re empowered to navigate the labyrinth of order management with confidence, positioning your business for success in a competitive landscape.
Outbound Management: Elevating Order Fulfillment
The outbound journey of your products is a pivotal phase, where streamlined processes translate to reduced order fulfillment time and enhanced customer satisfaction. Our Warehouse Inventory Systems redefine outbound management, seamlessly integrating picking, packing, staging, and shipping activities. This orchestration translates to heightened order throughput, elimination of inventory backflow, and a streamlined outbound process that sets the stage for operational excellence.
In Conclusion: Embrace Efficiency with AutoPower’s Warehouse Inventory Systems
As the automotive industry hurtles forward, businesses find themselves at a crossroads – a juncture defined by transformative technologies and a ceaseless pursuit of efficiency. AutoPower’s Warehouse Inventory Systems offer a comprehensive solution, poised to elevate your operations, minimize errors, and amplify productivity. From advanced inbound management to the precision of barcode systems, from order management insights to streamlined outbound processes, our WMS stands as a testament to innovation, reliability, and operational excellence.
With AutoPower’s Warehouse Inventory Systems, you’re not merely embracing a solution; you’re embracing a transformative force that propels your business into a future defined by precision, efficiency, and strategic advantage. In a landscape where every action counts, choose the path that unlocks your warehouse’s true potential – choose AutoPower’s Warehouse Management Systems and embrace a future where efficiency isn’t just a goal; it’s an unwavering reality.
Warehouse Space and Activities Optimization Basically, this practice is about optimization of the warehouse layout based on activities. The concept is to position activities with a lot of movement between them close to each other. Whether operating an existing warehouse or preparing for a new distribution center, an efficient layout and workflow plan (developed from an in-depth analysis) is an essential element of an effective distribution center and warehouse operations. The goal in optimizing warehouse operations is to design work flow paths that minimize total travel distance, mitigate congestion, open sight lines, maximize storage density and conform to physical site restrictions. While that was easy to say, let’s focus on areas that will have the greatest impact on your operations. Tangible proven improvements come from focusing on areas of waste and implementing
Warehouse Space and Activities Optimization
Basically, this practice is about optimization of the warehouse layout based on activities. The concept is to position activities with a lot of movement between them close to each other. Whether operating an existing warehouse or preparing for a new distribution center, an efficient layout and workflow plan (developed from an in-depth analysis) is an essential element of an effective distribution center and warehouse operations. The goal in optimizing warehouse operations is to design work flow paths that minimize total travel distance, mitigate congestion, open sight lines, maximize storage density and conform to physical site restrictions. While that was easy to say, let’s focus on areas that will have the greatest impact on your operations. Tangible proven improvements come from focusing on areas of waste and implementing corrective solutions.
Problem areas of waste in warehouse operations are:
• Space – Usually, the use of warehouse space is less that optimal. Racking systems are not aligned with the expected parts/product flow.
• Movement – The unnecessary movement of personnel, walking, reaching, searching due to inefficient layout for put-away and picking processes.
• Overstocking – Delivery and storage of parts before they are needed.
• Waiting – Personnel delayed at picking lanes, replenishment areas, receiving and shipping areas all slow the fulfillment of orders to customers.
• Returns – Activities that cause rework, returns or adjustments caused by discrepancies, damaged, defective, or mislabeled inventory.
• Poor Storage Logistics – Internal practices that store fast moving inventory in a less than optimal location that adds labor cost and lowers productivity. Some Best Practices being applied to these problems are:
• Warehouse design outline.
◦ Determine high-level space requirements for all warehouse functions like:
Storage – Pallet Racking, Mezzanine, Vertical Lift Modules etc.
Docks – Loading docks to load and unload inventoried items
Staging – Location where inventoried items are staged for processing
Picking – Warehouse function and zones to collect inventoried items
Packing – Warehouse function and area for packing orders to ship
Returns – Area where returned inventory items are staged for processing
Aisles – Areas of passage designed for people and equipment
Showroom – POS and/or pickup “will call” area may support inventory
Large assemblies’ storage area – Large typically heavy item storage
Offices – Office space for staff and warehouse management
Restrooms – Staff and warehouse management bathrooms
Support Areas –Training/Break Rooms, Utility/Equipment Rooms etc.
◦ Utilize Smart Storage by assigning activities related to parts with longer storage requirements to high-shelf space and high-volume parts with labor intensive processes to low-shelf space
◦ Locate functions near high velocity product (like staging, packing and shipping) close to one another
◦ Determine a high-level flow design
Hot Pick Zones
Smart Put-Away, Smart Picking
◦ Assign optimal parts handling methods to each work flow path
◦ Document expansion and contraction strategies
Problem areas of waste in warehouse operations are:
• Space – Usually, the use of warehouse space is less that optimal. Racking systems are not aligned with the expected parts/product flow.
• Movement – The unnecessary movement of personnel, walking, reaching, searching due to inefficient layout for put-away and picking processes.
• Overstocking – Delivery and storage of parts before they are needed.
• Waiting – Personnel delayed at picking lanes, replenishment areas, receiving and shipping areas all slow the fulfillment of orders to customers.
• Returns – Activities that cause rework, returns or adjustments caused by discrepancies, damaged, defective, or mislabeled inventory.
• Poor Storage Logistics – Internal practices that store fast moving inventory in a less than optimal location that adds labor cost and lowers productivity.